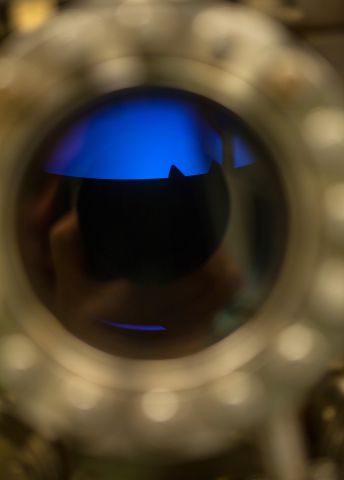
Project Grant 2015
The Boride Frontier – Pioneering materials development of multifunctional metal diboride films by new PVD processes
Principal investigator:
Johanna Rosén, Professor in materials physics
Co-investigators:
Per Eklund
Per Persson
Institution:
Linköping University
Grant in SEK:
SEK 37.5 million over five years
Borides are compounds consisting of the element boron and one or more metals. They are used in the manufacture of aircraft and spacecraft, for example, precisely because they are so hard. But researchers have not yet been particularly successful in producing really thin boride films, more accurately known as diborides – compounds in which each molecule consists of two boron atoms, combined with one or more metal atoms. Films of this kind would offer dramatic new potential.
The result could be coatings with a fantastic ability to protect or cut through other materials. But there is the added potential of materials with new, previously unknown properties. That potential will be offered if the researchers create new boron-metal alloys, and also if they succeed in making the borides so thin they are no longer even called films; they are referred to as “2D materials”. These materials are no more than a few layers of atoms thick, just like the carbon allotrope graphene – whose properties are quite different than those of the other carbon allotropes graphite and diamond.
Revolutionary new materials based on current knowledge
To date, research into hard film materials has focused primarily on oxides, nitrides and carbides – compounds containing oxygen, nitrogen and carbon. This goes for Linköping University too.
“We’ve been researching on this for twenty years, and we’ve come a long way. But why not use all the knowledge we have accumulated to research into a completely new materials system? We’re very well placed to tackle the challenges posed by borides,” explains Johanna Rosén, who is a professor at Linköping’s Thin Film Physics division, and is heading the boride project. The project involves around ten of the university’s researchers, soon to be joined by the same number of PhD students and postdocs.
The challenging part is to manufacture the borides themselves. Boride films tend to be unstable, and react with oxygen. There may be tensions in the material, and the films are reluctant to adhere to the surface.
“We are still missing many pieces of the puzzle, so the field hasn’t really taken off yet. We need to develop new methods and processes that are optimized for borides,” says Rosén, who says the funding from the Knut and Alice Wallenberg Foundation has made this work possible.
Examining each step in minute detail
The researchers in Linköping make their films using vapor-based methods. They start off with a sheet of the metal diboride from which they want to make a film. The sheet is treated in a vacuum: it may be bombarded with ions or subjected to a powerful electric current. This causes atoms in the material to disconnect from one another and form a vapor. Particles in the vapor then transfer to a surface, where they form the thin film.
The team includes researchers with specialist knowledge of all the stages of the process. Some work theoretically, using the university’s supercomputer to simulate the new materials.
“Many borides are made up of alternating layers of boron and a metal. Different metals produce very different properties – the boride may be anything from super hard to superconductive. We can use simulations to experiment with different mixtures,” Rosén comments.
When the vapor has been made, the team’s plasma physicists examine it in detail to work out whether its properties are suitable for thin film manufacture, or whether modifications are needed. When the thin films take shape, other researchers study them, their atomic structure, conductivity, hardness and many other properties.
“We know about the theoretical properties of the material, but we don’t know whether it will be as beautiful and well-organized in reality. We can find explanations for the properties of the material by examining its atomic structure,” Rosén explains.
Not just the material, but the process
It is essential that the raw material is as clean as possible. Rosén mentions that even materials bought from globally renowned suppliers may have impurity levels of up to ten percent.
“But we are working closely with our supplier, who has now understood what we need. This research project is different from others – the fact that we can focus so much on developing the process, all the way from developing the basic material to studying how manufacture could be scaled up to industrial level.”
Extremely hard materials are needed to cut aluminum, for example – a soft metal that can easily become “sticky”, and is used in large quantities by industry. But Rosén is just as keen to explore more unexpected applications. Perhaps the big breakthrough will instead be made in electronics.
“A few months ago we made a 2D carbide that turned out to have world-record capacitance, i.e. the ability to store an electrical charge. We thought it would have good properties, but they were really good. It made be curious: What kind of amazing properties will we get if we make metal diborides in 2D? It’s a real voyage of discovery, which is one of the really fun aspects of my research.”
Text Lisa Kirsebom
Translation Maxwell Arding
Photo Magnus Bergström